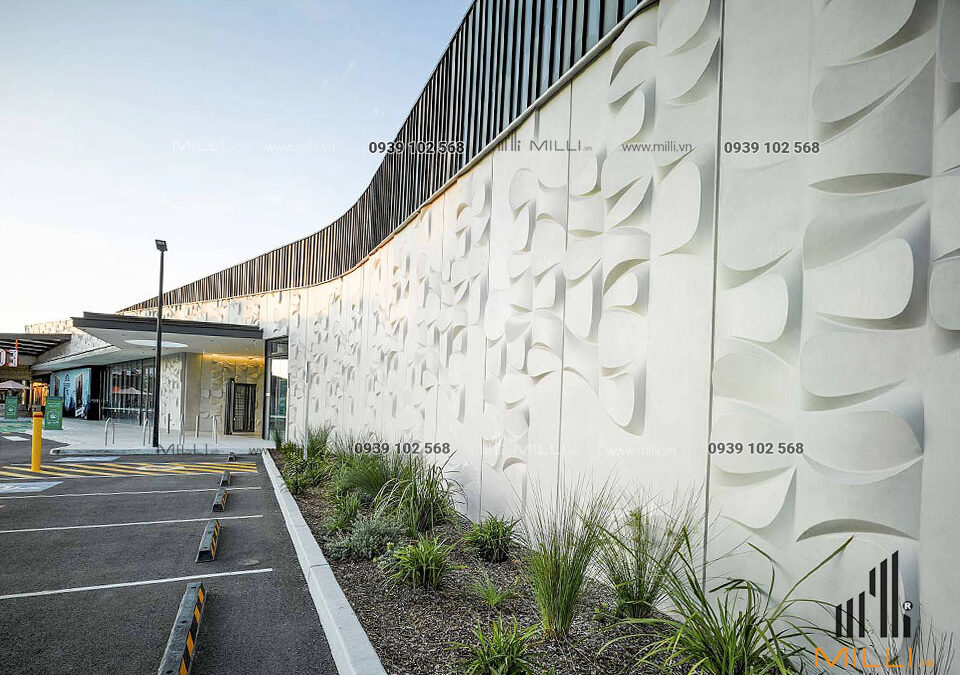
GFRC cladding decorates impressive and novel building facades
GFRC Cladding has become more and more popular choice as an architectural finish material. People consider Glass reinforced concrete cladding as a relatively new type of construction material. Although, the construction industry has been using it for over 50 years it’s only getting more attention in the 21st century. GFRC cladding is very versatile and that is why it’s gaining popularity among architects and specifiers. Due to its high elastic properties designers use GFRC cladding in solutions where resistance to live loads is necessary.
GFRC cladding systems require high quality standards in manufacture and meticulous record keeping. If you use glass fibre reinforced concrete cladding or panels in your projects. It is important to employ subcontractor or installation crew with GFRC cladding experience.
Follow the article below of MILLI TILES for more detailed information about this material!

What is GFRC?
GFRC materials are known in the modern construction industry by many different names: Glass Fiber Reinforced Concrete (GFRC), Verre Cement Mixture (CCV), Fiber Reinforced Concrete. This is a new construction material, produced by injection molding and machine injection from a mixture of fine aggregates: cement, clean sand, clean water, alkali resistant fiberglass and plasticizers. GFRC materials have high durability, diverse shapes, beautiful designs, natural colors… have become materials that play an important role in the economy. Technology and aesthetics of the construction industry worldwide. GFRC is applied in construction works in details such as: GFRC facades, GFRC moldings, GFRC column tops and garden and art decoration products.
The fibers serve a purpose similar to the reinforcing steel in reinforced concrete, which is placed primarily in tensile stress areas. Because the glass fibers add flexural, tensile and impact strength, Architectural panels made from GFRC are strong, durable, and lightweight.
GFRC cladding are finding wide spread use in the restoration and renovation of historic buildings. And are considered by many to be the best solution available for the repair and replacement of terra cotta tiles that are deteriorating under the influence of time and weather.

Where are GFRC Cladding used?
GFRC cladding are widely use as the exterior facade material in the construction or renovation of many types of commercial and institutional buildings. They are available as wall units, window wall units, spandrel, mullion, and column covers. As well as for fascia panels, soffit, para pets, sunscreens, mansard roofs, and interior feature panels.
Each cladding is custom design for the specific application, and their largest dimension can be either vertical or horizontal. Panels 400 square feet and larger are possible, reducing production, shipping, and installation cost.
GFRC cladding is widely used today for both new building construction and for renovations of existing building facades. In renovations applications. GFRC cladding can often be installed directly over the old cladding with minimal superimposed load on the existing structure, and minimal upset to existing tenants and operations.
GFRC cladding is a new building material, which has more advantages than previous traditional building materials. Using GFRC materials brings practical benefits to investors and construction contractors when building works. So what are the advantages of GFRC material? Let’s learn the advantages of GFRC materials through the following article:
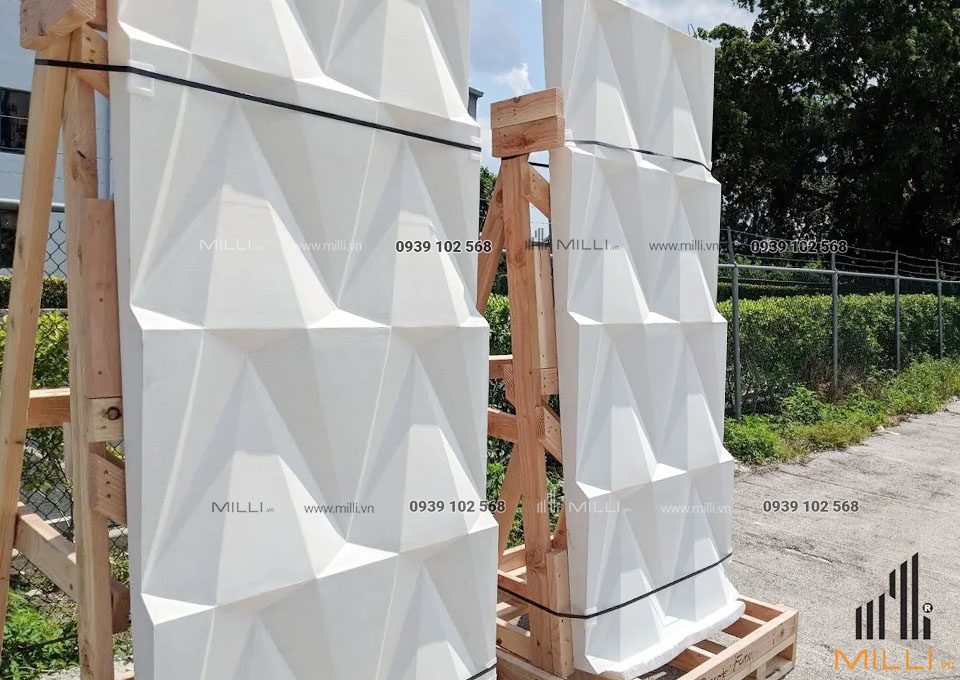
Advantages and Disadvantages of GFRC cladding
Light load
GFRC material is 75% lighter than traditional concrete, which reduces the load on the building, reduces transportation costs and is easy to install.
GFRC cladding have high bearing strength
Compressive strength: 50-80 MPa, Bending strength 20-30MPa as well as having a high strength-to-weight ratio. The GFRC components used to construct lightweight panels are non-flammable minerals. In addition, the face coat of concrete protects against fire and acts as a temperature regulator.
Create a variety of shapes
GFRC molded or injection molded easily creates products with diverse shapes, including complex designs such as: folded, bent, wavy. GRC is suitable for complex architectural styles that require high sharpness and meticulous decoration.
GFRC cladding good durability
GFRC does not have surface cracks, even large products, is waterproof, and is not affected by the impact of the environment. This strength is increasingly being applied effectively thanks to the use of low alkaline cement and puzolan admixture.
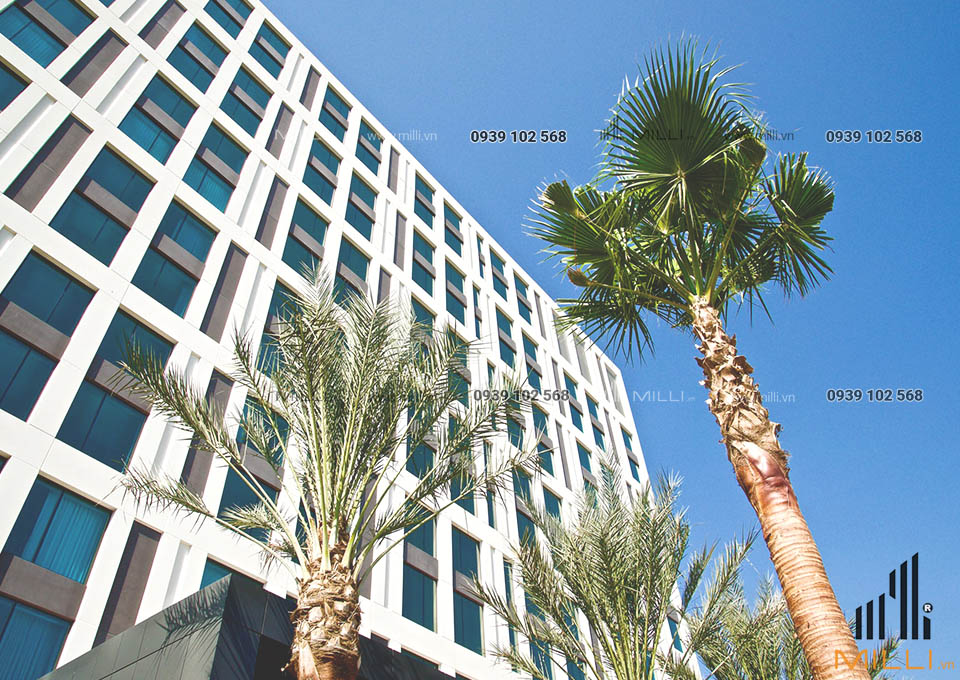
Beautiful natural colors
GFRC cladding has a beautiful natural color due to the use of natural sand and the spraying process makes the surface layer without air holes or any voids.
High adaptability
GFRC is highly adaptable, suitable for all architectural styles. GFRC products are widely used in facade decoration, architectural details, interior decoration to garden landscape decoration.
Sustainable, eco-friendly
GFRC uses less cement than conventional concrete and significantly recycled materials are use, so GFRC is very sustainable and environmentally friendly. Due to the fiber coating of GFRC, the alkali-resistant fibers act as extra protection. The resulting panels resist rain, moisture, alkali attack, corrosion, or other environmental issues.
The mechanical properties of GFRC cladding make it ideal for various requirements. However, one potential disadvantage for some users is the cost of GFRC. GFRC cladding can be expensive to use when compared to ordinary concrete. Of course, the added cost comes with additional strength and several other benefits, already mentioned in previous sections.
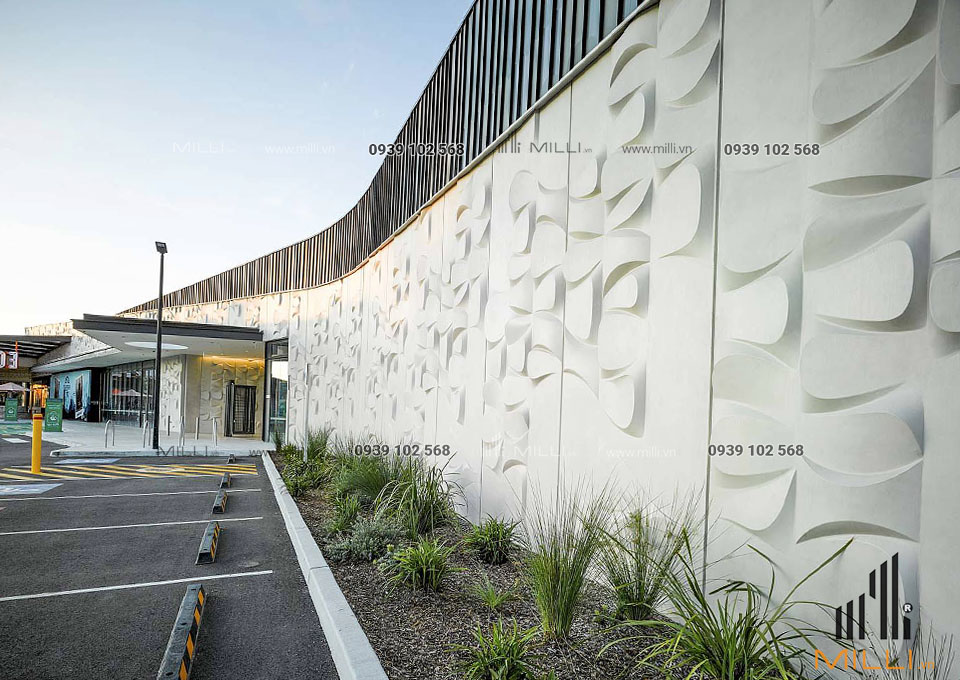
The Basic Uses of GFRC cladding
There are many applications and projects where glass fiber-reinforced concrete is the ideal choice. Some of these applications are:
Facade GFRC: Facade decorative GFRC cladding have good fire resistance and absolute waterproofing. In addition, GRC façade is less affected by weather, retains its original color and minimizes maintenance costs. Application of GRC facade helps the building keep its beauty over time.
Concrete Countertops: GFRC countertops are becoming more and more common today due to their high aesthetic appeal and crack resistance. Color pigments can make countertops match the required color.
Wall cladding: GFRC wall cladding provides a beautiful look while reducing the overall weight. These panels are long-lasting as well as decorative for home and office interiors.
Concrete Dining Tables: Nowadays, it is common to see concrete dining tables in restaurants and houses. The concrete for these dining tables is GFRC due to its lightweight nature and high sheen. In many cases, integrated countertops and dining tables create a beautiful kitchen island design.
Outdoor Furniture: GFRC is resistant to adverse environmental conditions. Therefore, GFRC furniture, such as tables, benches, and chairs, is an excellent choice for outdoor places like parks.

How are GFRC cladding manufactured?
Glass Fiber Reinforced Concrete (GFRC) is made by using the following materials:
- Fine Sand: The fine sand should be 0.4 mm to 0.5 mm, and the accepted range is 0.3 mm to 0.6 mm. Finer particles decrease the flowability of concrete, and coarser particles can be deflect after striking the surface during spraying.
- Cement: Ordinary Portland cement is acceptable for making glass fiber-reinforced concrete. The weight of cement is usually equal to the weight of the sand used.
- Polymer: There are many types of polymer and concrete matrix mixtures, such as Ethylene Vinyl Acetate (EVA), Styrene Butadiene Rubber (SBR), and Acrylic polymer. Acrylic polymer is the preferred choice for glass fiber-reinforced concrete. The weight ratio of polymer to concrete is usually 6 grams of solid polymer per 100 grams of the cementitious mixture.
- Water: The water content in the concrete mix is critical, as too much water can ruin the mixture. It is essential to consider the water content of the polymer mixture to determine the overall water content. The ratio of total water to concrete should fall between 0.30 to 0.35.
- Admixtures: Manufacturers produce various admixtures to use in GFRC. Common admixtures are silica fumes and superplasticizer.
- Glass Fibers: The addition of chopped-up alkali-resistant (AR) glass fibers is the defining factor of glass fiber-reinforced concrete. The amount of glass fiber will vary based on the type of manufacturing method used, as discussed below.
- Sand, cement, polymers, water, and admixtures are also common in other types of reinforced concrete. GFRC is unique in terms of materials because of the addition of glass fibers.

There are three manufacturing methods for Glass Fiber Reinforced Concrete Cladding:
Spray – up GFRC
Spray-up GFRC is the conventional way to create precast concrete panels. In this method, the Glass Fiber Reinforced Concrete is spray into a mold by hand.
A concentric chopper spray gun is use to spray long glass fibers into the concrete mix. The mixing occurs in the gun’s nozzle.
On average, this method contains a glass fiber content of about 5%, a higher fiber content than the usual concrete premix. This method requires skilled labor to be successful, and good quality equipment and quality checks of the work in progress.
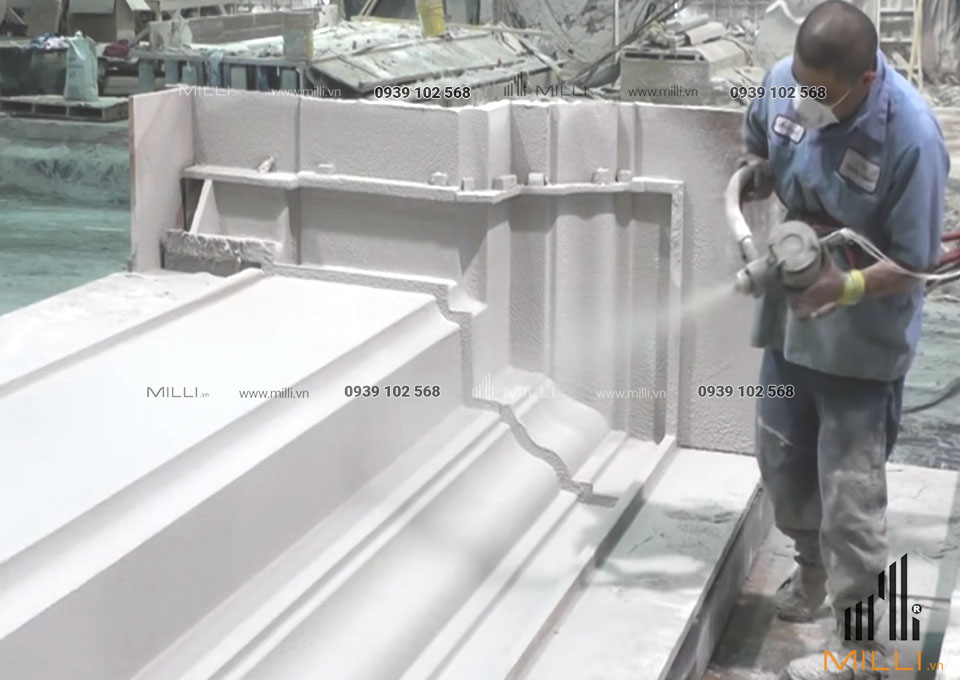
Vibration Casting
The defining factor of vibration casting is the use of premix concrete. The premix concrete mixture is poured into a mold. Then the mold is vibrated so that the concrete achieves consolidation.
This method is simpler and cheaper than sprayed GFRC. However, the molds in this method should be water tight. Vibration casting should not be use with rock molds.

Hybrid Casting
Hybrid casting is the combination of spray-up and the use of a premix. A specialized spray head using a peristaltic pump is used to spray the concrete.
Hybrid casting introduces the benefits of spray-up GFRC and vibration casting. While sprayed GFRC requires highly skilled labor, hybrid casting is possible with moderate skill.
Due to using a spray instead of vibrations for the premix, the strength of the resultant concrete panel is higher than the vibration casting methods.

Why should use GFRC cladding instead of precast concrete panels?
Weighing up to 80% less than architectural precast. GFRC cladding materially reduces the weight and cost of the foundation, footings, and structural framing needed to support multi-story buildings. This enables the owner to reduce overall construction costs and accelerate schedules without sacrificing the durability or the architectural aesthetic of precast concrete fabrication.
GFRC cladding does not crack due to the process used for making GFRC. Instead of directly pouring a fluid concrete mixture into a mold. GFRC is spray into the mold by special sprayers. Spraying makes the GFRC more adhesive and resistant to cracking in the short or long term.

How much does GFRC cladding cost?
The cost of GFRC depends on many factors, such as:
- Whether you want GFRC precast or GFRC premix. Precast GFRC comes in a ready-to-install form matched to your required shape. In the case of GFRC premix, you will need to hire an expert who can use it correctly. Correct proportions and casting methods are crucial, and the tiniest oversight may ruin the final result.
- The GFRC manufacturing method. Hybrid, sprayed, or vibration casting? Hybrid is the go-to choice for most people since it offers a good balance between price and strength.
- The thickness and area of the GFRC panels.
The cost of GFRC cladding generally comes as a price per square foot for a given thickness of GFRC. For an accurate idea about how much GFRC will cost youper square foot. The Installation cost of GFRC panels will vary based on the average panel size, accessibility to building connection points, building site location and availability and type of cranes required.

MILLI TILES – Don’t let obstacles stop you from creating creative masterpieces
Milli Tiles – The unit that supplies and constructs GFRC cladding for projects. . If you need strong and lightweight concrete, precast GFRC cladding could be the ideal material for your project. You can contact MILLI TILES to learn about different GFRC products and at the same time we also accept GFRC construction for projects. Please contact us today for advice on GFRC cladding products!
MILLI CONSTRUCTION MATERIAL COMPANY LIMITED
📱 Hotline: 0939 102 568 📞
We will quote a specific % discount for you depending on the quantity or total value of the order
Contact us to order today, to get the best price support.
Instructions for construction of wind cement bricks, you can read and download below:
FILE INSTRUCTIONS FOR Brick Construction, DOWNLOAD HERE
Contact: Zalo: 0939 102 568
Fanpage: https://www.facebook.com/gachbonggio.hcm/
Youtube: https://www.youtube.com/channel/UC-ePtN2lIBwSp13ADgW7LSA