GFRC moulds is key to advancing towards a fully automated and digital process for complex geometry GFRC. Existing mould systems are not sufficiently flexible to meet the demands of today’s requirements. Therefore a new method to produce the mould must be developed
Concrete is used in a wide range of applications. Most construction projects utilize concrete, from the walls and roofs of buildings to thick dams to mind-blowing skyscrapers.
Due to the variety of applications, many different forms of concrete have developed. These concrete forms differ vastly in terms of their physical properties, appearance, usability, benefits, and many other factors.
One of the most popular forms of concrete is Glass Fiber Reinforced Concrete (GFRC). It is a significant improvement over traditional concrete and has been steadily replacing it in countless cases. In order to make products easier and faster to produce, the GFRC moulds with different sizes and designs were born. Aim to best meet the production process.
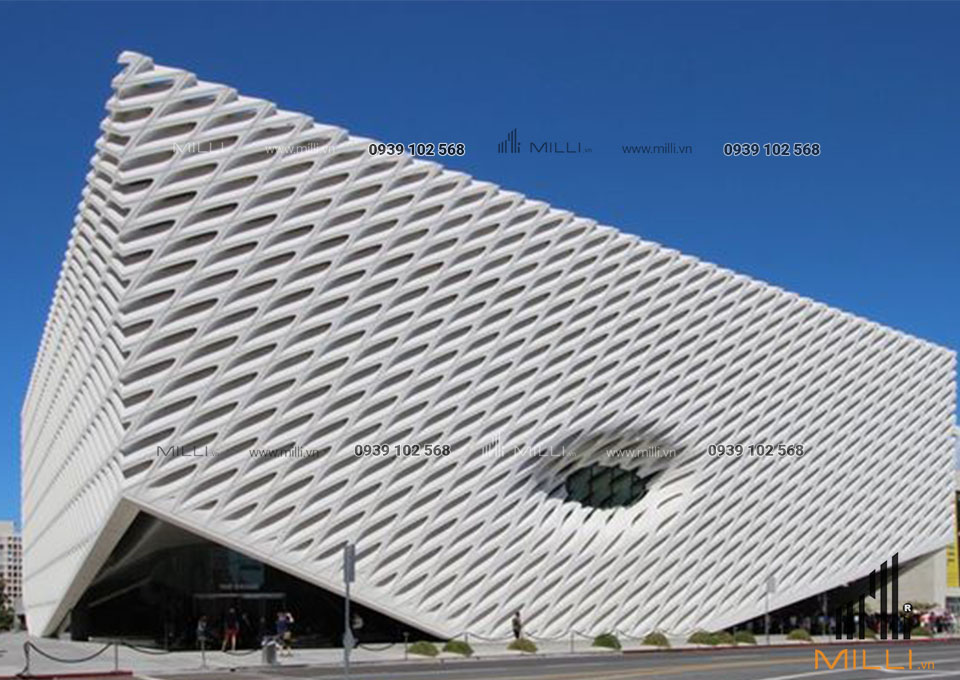
What is Glass Fiber Reinforced Concrete?
GFRC stands for Glass Fiber Reinforced Concrete. This type of fiber-reinforced concrete contains glass fibers. The concrete matrix binds to these glass fibers, and the addition of glass fibers leads to improved reinforcing and mechanical properties of the concrete and higher tensile strength.
GFRC weigh less than traditional concrete panels but are stronger; hence, their popularity when additional reinforcement is necessary. Therefore, using a thinner GFRC panel instead of a bulkier panel with steel reinforcing bars leads to a saving in space.
Development of a new GFRC moulds system
Generating the GFRC mould is key to advancing towards a fully automated and digital process for complex geometry GFRC. Existing mould systems are not sufficiently flexible to meet the demands of today’s requirements. Therefore a new method to produce the mould must be developed. The method described in Henriksen, Lo, & Knack, (Citation press) only addresses the mould systems using premixed thin-walled GFRC. Therefore a variation has been developement that allows the production of complex geometry thin-walled GFRC using the sprayed method while simultaneously allowing an edge-return.
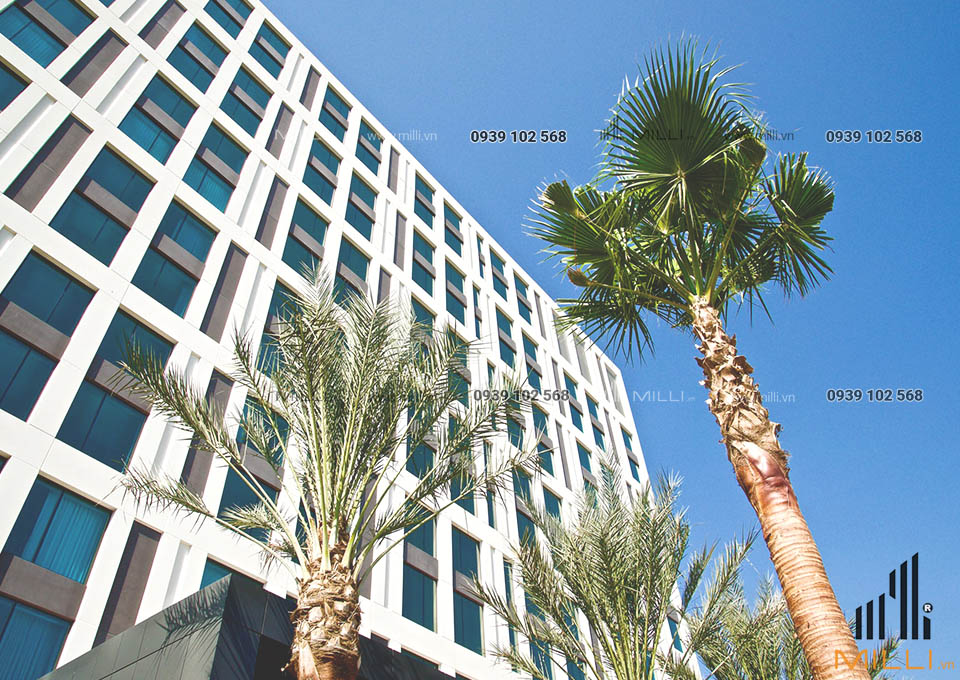
Advantages of manufacturing GFRC materials by moulds
The production of the new GFRC mould is the first stage of the production process for complex geometry GFRC. This method will enable unique complex geometry-shaped foam to be cast with the possibility of an edge-return that can be used as moulds for GFRC panels. The method enables a faster mould production method for GFRC than the current CNC milling solution and enables the re-use of the flexible table to produce many foam moulds.
While the foam mould replicates the surface generated on the flexible table, it does not allow for an edge-return if a GFRC panel was cast directly onto it. In principle it would be possible to use a silicone band to mark the boundary of the panel but when the fibre concrete mix is spray this would only allow for a panel with a constant thickness and not permit an edge-return that protrudes from the back surface of the GFRC panel.

The new GFRC moulds system allows the concrete to cure for 28 days on a more cost-effective foam mould, rather than leaving it on the flexible table to cure. This leaves the flexible table free to be used to produce further moulds rather than remaining unused during the 28-day curing process.
The process for producing the new GFRC moulds has been patent and contributes significantly to the development of a novel fully automated and digital design and manufacturing process for complex geometry thin-walled GFRC. This would allow the production of panels at a lower cost combined with increased production speed and higher finished surface quality.
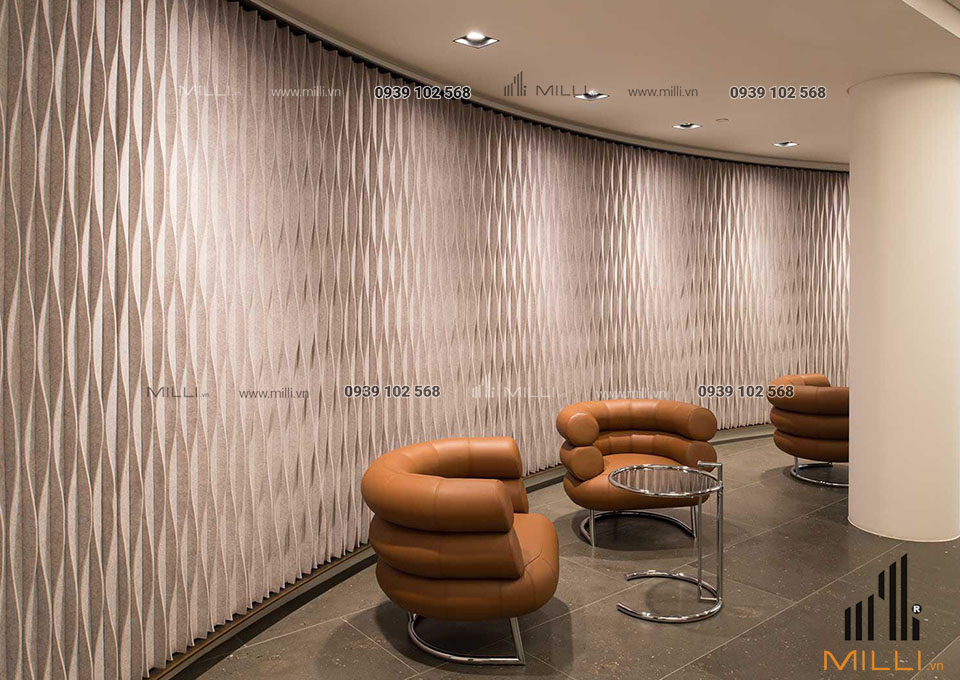
Disadvantage of GFRC moulds
The limitation of the GFRC moulds is that it is restricted to the size of the flexible table and that the edge-return must be project from the surface. The next steps will be to test the mould with the GFRC cast on the mould. Additional research must to be done to development the mold system to allow for edge-returns that are normal to the surface. And potentially edge-returns with variable angles to the surface.

Classification of GFRC moulds
Typical formwork in GRC production is usually made from plaster, clay, silicon, plastic, foam or wood. These are the components used to create molds when producing GRC materials. Depending on each products requirements, we have different GRC production molds. The following are commonly used GRC production molds:
- Wood moulds pattern: usually used for products with few details or that do not require sharp details such as flat wall panels or panels with few decorative details.
- Silicone moulds: often used for products with many intricate and sharp decorative details. To create a silicone mold, we first put the ingredients into the mold, then use a spacer to fix the mixture, and then add silicone or rubber. Often silicone formwork is used to produce reliefs or statues.
- Moulds manufactured by CNC cutting technology: made from foam or wood or cut from silicone or rubber. Using CNC cutters, this formwork can produce extremely precise flat panels.
GFRC production moulds help save costs because they produce finished architectural products right from the first time. The products GRC creates are very diverse but uniform to every little detail. In addition, for works that need repair, we can rely on damaged parts to produce suitable formwork. Moreover, the formwork can be reused for subsequent projects, or to be reassembled for a larger architectural product.

How do GFRC manufacturers make GFRC materials?
There are three manufacturing methods for Glass Fiber Reinforced Concrete:
Spray-up GFRC
- Spray-up GFRC is the conventional way to create precast concrete panels. In this method, the Glass Fiber Reinforced Concrete is spray into a mold by hand.
- A concentric chopper spray gun is uses to spray long glass fibers into the concrete mix. The mixing occurs in the gun’s nozzle.
- On average, this method contains a glass fiber content of about 5%. A higher fiber content than the usual concrete premix. This method requires skilled labor to be successful, and good quality equipment and quality checks of the work in progress.
Pros: Allows for very high fiber loads using long fibers resulting in greatest possible strength.
Cons: Requires expensive, specialized equipment (generally $20,000 or more).

Vibration Casting
- The defining factor of vibration casting is the use of premix concrete. The premix concrete mixture is pours into a mold. Then the mold is vibrate so that the concrete achieves consolidation.
- This method is simpler and cheaper than sprayed GFRC. However, the molds in this method should be watertight. Vibration casting should not be uses with rock molds.
Pros: Less expensive than spray-up, although a special spray gun and pump is require.
Cons: Fiber orientation is more random than when using spray-up and fibers are shorter resulting in less strength.

Hybrid Casting
- Hybrid casting is the combination of spray-up and the use of a premix. A specialized spray head using a peristaltic pump is use to spray the concrete.
- Hybrid casting introduces the benefits of spray-up GFRC and vibration casting. While sprayed GFRC requires highly skilled labor, hybrid casting is possible with moderate skill.
- Due to using a spray instead of vibrations for the premix. The strength of the resultant concrete panel is higher than the vibration casting methods.
Pros: Affordable way to get start. A hopper and air compressor run about 400$ – 500$. Much less than the spray guns used for spray-up or premix.
Cons: Since the face coat and backer mix are applies at different times careful attention is need to ensure the mixes have a similar makeup to prevent curling.

Why should GFRC materials be manufacture using GFRC moulds?
- GFRC moulds can be use which reduces cost and fabrication time compared to previous production
- A face coat without fibers can be spray to avoid visible fibres in the surface of the panels.
- Secondary support structure can be integrated in panel to reduce the GFRC material.
- The fiber orientation of the GFRC can be control using the sprayed method.
- The thickness of the panel can easily be varied dependent on requirements and local reinforcements.
- Support anchors can be sprayed into the panel and reinforced locally.
- The GFRC panel can be reinforce locally, adding sprayed fibers perpendicular to the tension stress in the material.
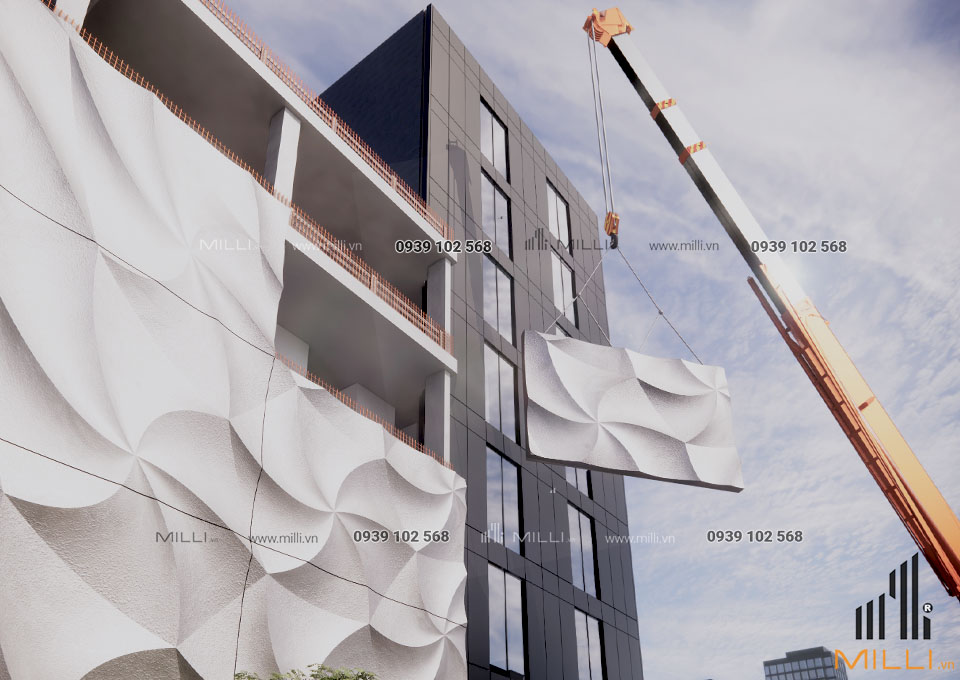


MILLI TILES – RECOGNITION OF GFRC MATERIALS FOR BIG, PRESTIGE, QUALITY PROJECTS
The birth of GFRC moulds manufacturers is extremely reasonable. There are now many builders and architects who are aware of the properties of GFRC and use this concrete mix in their structures. If you need strong and lightweight concrete. Precast GFRC could be the ideal material for your project. You can contact MILLI TILES to learn about different GFRC products and at the same time we also accept GFRC construction for projects. Please contact us today for advice on GFRC products!
MILLI CONSTRUCTION MATERIAL COMPANY LIMITED
📱 Hotline: 0939 102 568 📞
We will quote a specific % discount for you depending on the quantity or total value of the order
Contact us to order today, to get the best price support.
Instructions for construction of wind cement bricks, you can read and download below:
FILE INSTRUCTIONS FOR BRICK CONSTRUCTION, DOWNLOAD HERE
Contact: Zalo: 0939 102 568
Fanpage: https://www.facebook.com/gachbonggio.hcm/
Youtube: https://www.youtube.com/channel/UC-ePtN2lIBwSp13ADgW7LSA